What is Digital Twin and How Does It Work?
What is Digital Twin and How Does It Work?
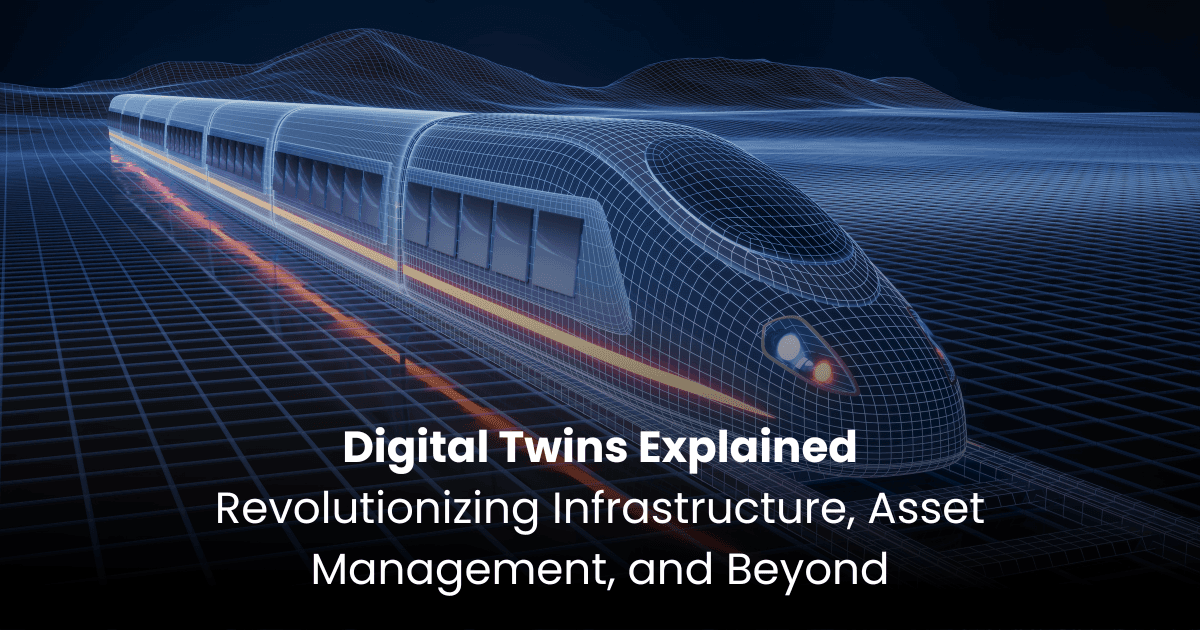
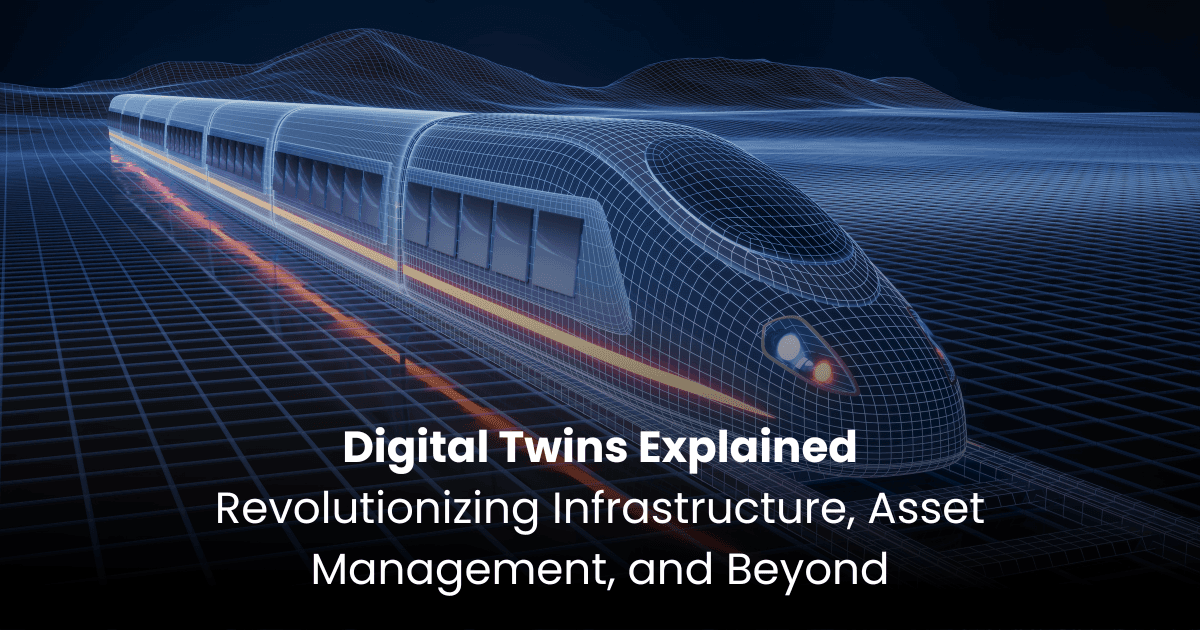
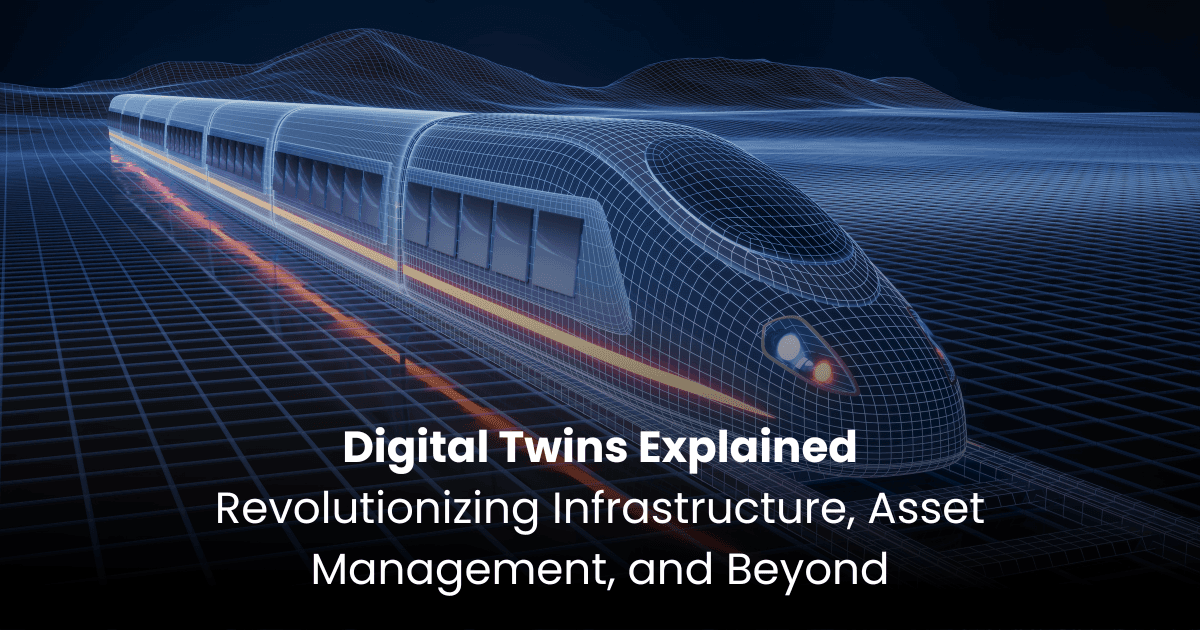
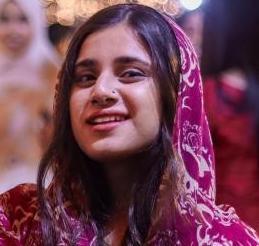
Syeda Narmeen Bukhari
Technical Content Writer
How many times have you wished you could find the optimum solution to a problem without having to try and err? Enter Digital Twin Technology - a revolutionary tool that creates real -time, dynamic replicas of physical systems allowing you to explore choices and predict outcomes with unparalleled accuracy.
The concept traces its roots back to NASA in the 1960s when they pioneered “mirroring technology” to create physical replicas of their space systems. In a landmark moment, the “Apollo 13” space mission in 1970 used fifteen simulators to virtually create and assess a moon-landing. As a result, the mission was aborted and the crew guided back to the safety of Earth. This was the first time in history that digital twin technology saved the day. Today, digital twins have evolved far beyond those early applications, transforming industries with real-time data integration and advanced analytics.
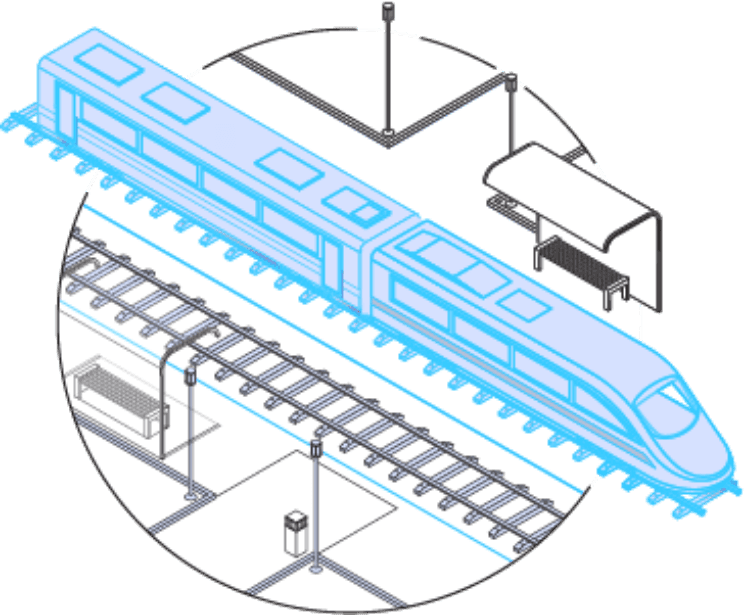
What is a Digital Twin?
A Digital Twin is more than just a virtual replica of real-world objects, systems, environments or even people. It’s a constantly evolving, real-time model powered by data from sensors, IoT devices, and advanced analytics. By mirroring its physical counterpart in a digitally curated environment, a digital twin enables organizations to simulate dynamic real-world scenarios, predict outcomes, and optimize performance.
What is a Spatial Digital Twin?
A Spatial Digital Twin takes this a step further by integrating spatial data into the digital model. Unlike a standard digital twin, it creates a location-based, highly detailed 3D representation of environments. Using tools like GNSS, LiDAR and camera technologies, spatial twins allow the capturing of the geometry, positioning and context of physical assets. This makes them invaluable for industries such as infrastructure, where precise spatial details are critical for decision making.
For instance, Kodifly uses spatial twins to model railway systems including tracks, tunnels, and surrounding vegetation. The technology not only mirrors physical structures but also provides actionable insights by analyzing real-time data.
How does Digital Twin Technology work?
The lifecycle of a digital twin starts with data collection. Sensors and IoT devices like LiDAR, cameras, and temperature gauges capture detailed real-world data about an asset’s structural performance, system operations, or environmental conditions.
This data is then transmitted via cloud platforms, edge computing, or wireless networks to centralized advanced software systems. The software processes and integrates the data to create an accurate digital replica (twin).
The twin is continuously updated with live data, ensuring it mirrors any changes in its physical counterpart. AI models analyze the data for patterns, inefficiencies, or potential anomalies. Insights from the analysis are then fed back into the system, allowing for constant refinement and optimization by creating a feedback loop.
This closed-loop system makes digital twins dynamic, allowing businesses to make proactive, data-driven decisions.
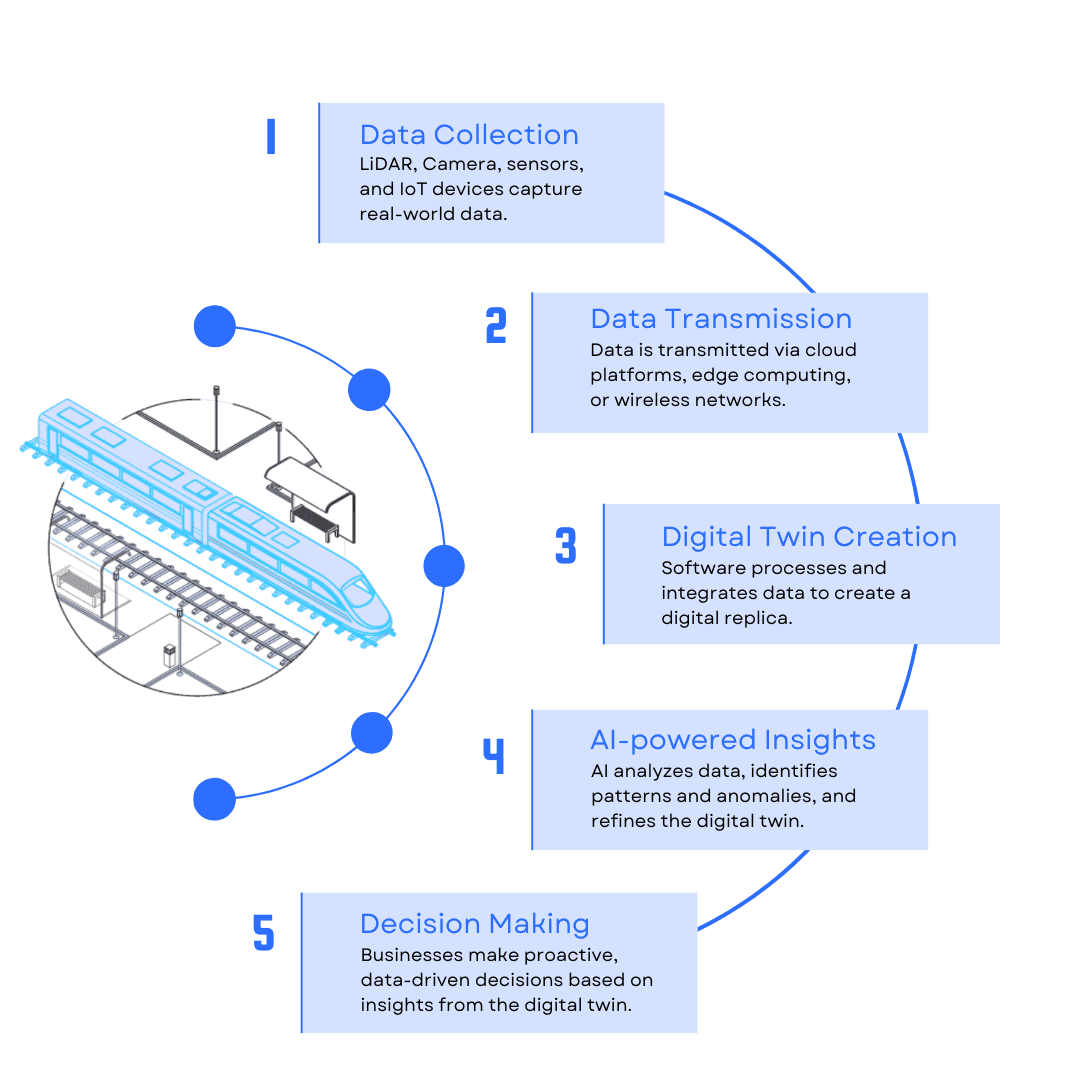
How is Digital Twin different from simulations?
While digital twins may sound similar to simulations, the two are fundamentally different. A simulation is a standalone model that tests specific scenarios and does not update in real time. A digital twin on the other hand, is a dynamic, real-time virtual replica that keeps getting updated, allowing for highly accurate predictions, identification of inefficiencies, and anticipation of failure (or success!)
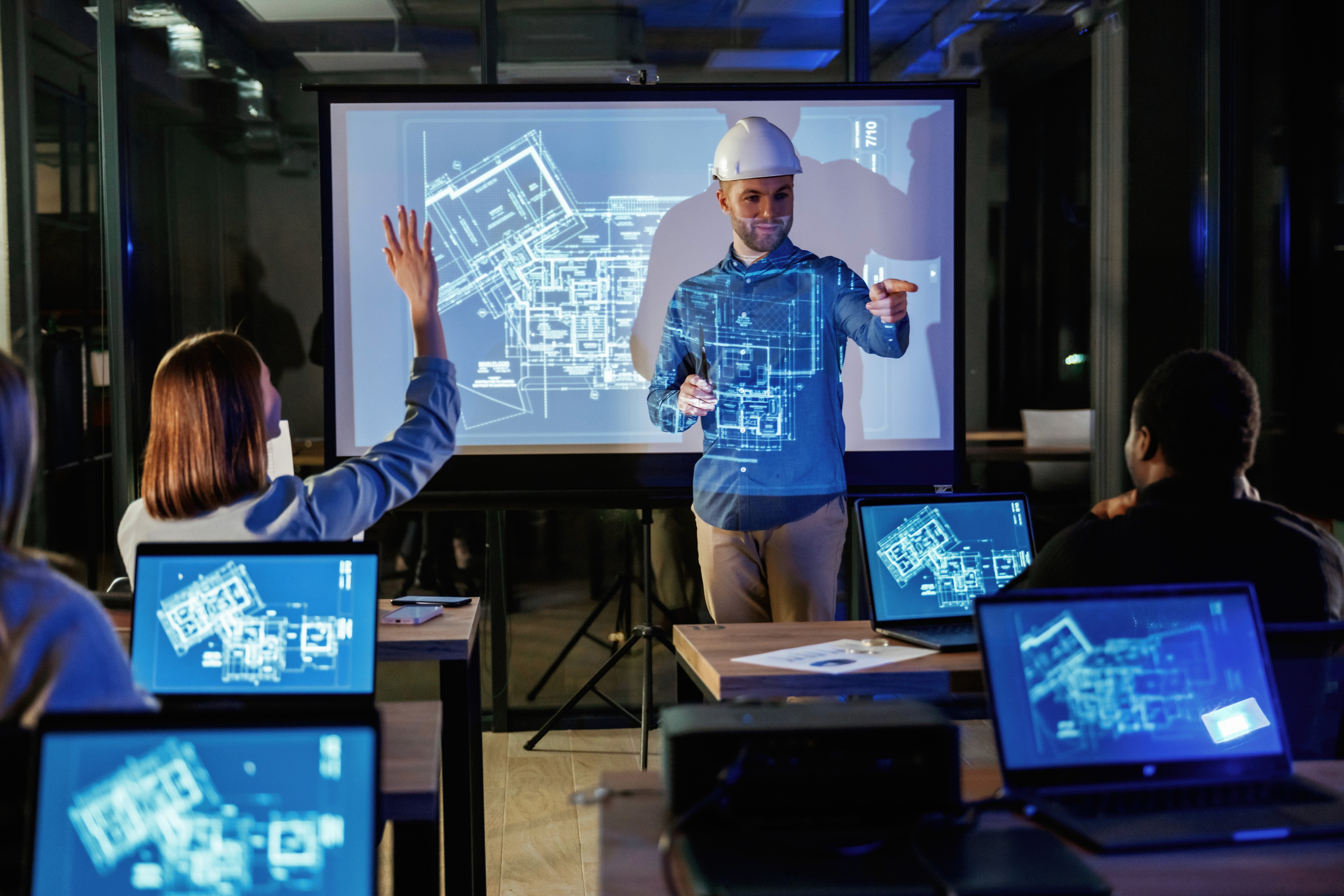
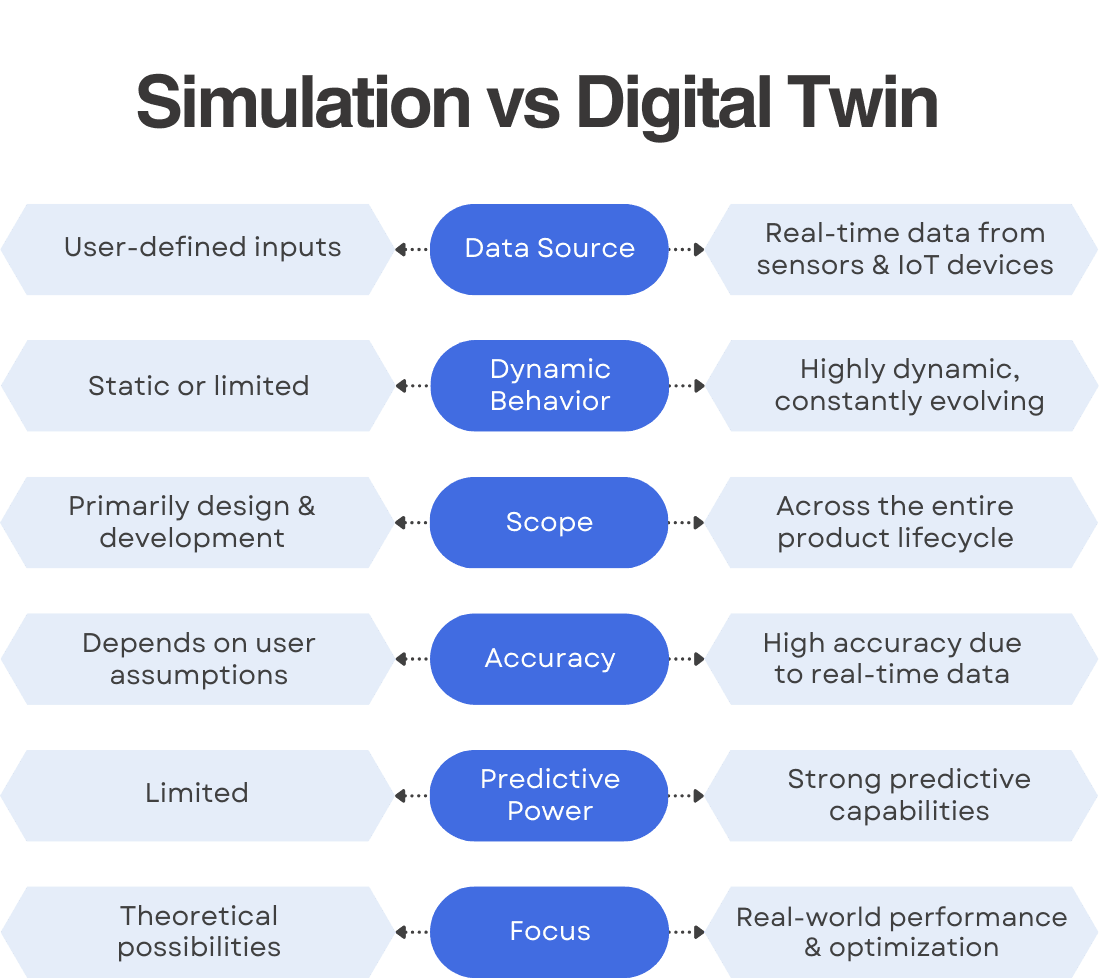
Where is Digital Twin technology used?
Digital twin technology spans a wide range of applications, proving its versatility and transformative potential. It encompasses various types, including Product Twins, System Twins, Data Twins, and Process Twins, each tailored to specific needs. From the initial ideation phase through engineering, production, control and monitoring the digital twin helps build and improve products and systems each step of the way.
In the manufacturing industry, digital twins test and validate new designs before they are sent to production, ensuring efficiency and reducing errors. The automotive, aerospace and defense industries are pioneers in making use of the digital twin for the ideation and development of successful new products. As industries evolve, the infrastructure and energy sectors are also poised to derive significant benefits from the technology. For instance, infrastructure projects can use digital twins to predict risks, enhance performance, and streamline operations, while energy systems may leverage them to optimize production and improve grid management.
By enabling improved performance, preemptive risk management and production optimization, digital twin technology is shaping the future of industries, offering tools to not only react to challenges but anticipate and address them proactively.
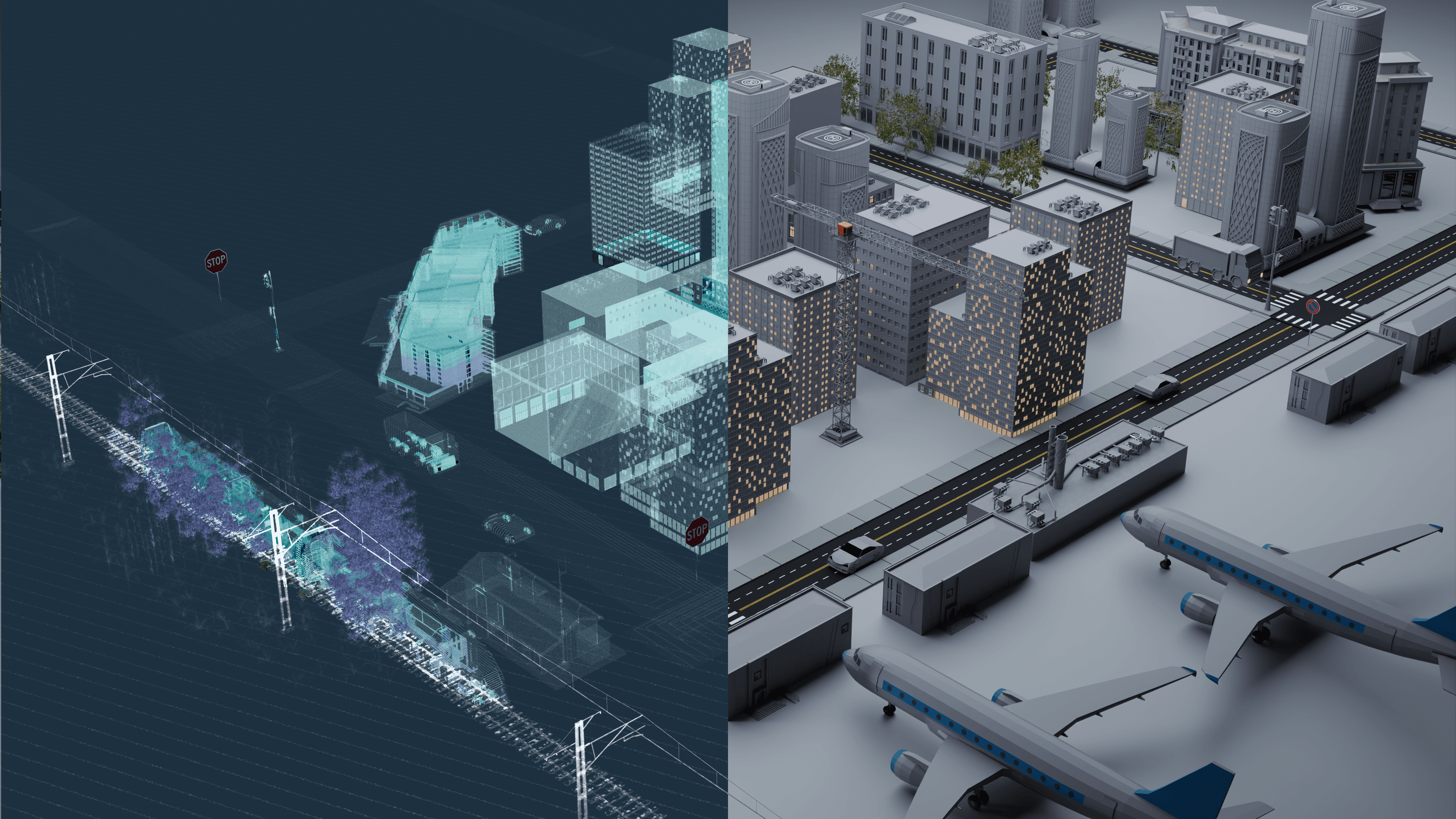
Kodifly leverages Digital Twin technology
Kodifly specializes in harnessing spatial digital twin technology to revolutionize infrastructure management in railways, highways, and airports. By integrating cutting-edge tools like LiDAR, GNSS positioning, and camera fusion technology, we provide transformative solutions for managing complex environments with precision and efficiency.
Kodifly’s SpatialSense Suite offers comprehensive solutions for capturing, processing, and analyzing spatial data. This platform combines inputs from LiDAR sensors, high-definition cameras, GPS, and IMUs to create highly accurate, real-time digital replicas of physical environments. These digital twins generate AI-powered actionable insights that empower infrastructure operators to make data-driven decisions, improve asset performance, and reduce maintenance costs.
For instance, Kodifly’s Railway Vegetation Management System is an advanced solution designed to ensure the safety and efficiency of railway operations by addressing vegetation-related challenges. Utilizing cutting-edge technologies such as LiDAR, AI-powered analytics, and GNSS positioning, the system provides railway operators with a comprehensive, automated approach to managing vegetation encroachment.
This system works by scanning and mapping the railway corridor in high detail, using LiDAR sensors to create precise 3D models of the surrounding environment. These models, combined with camera fusion technology, enable the system to identify vegetation intrusions that could interfere with the railway’s Kinetic Envelope (KE), signaling equipment, or power lines.
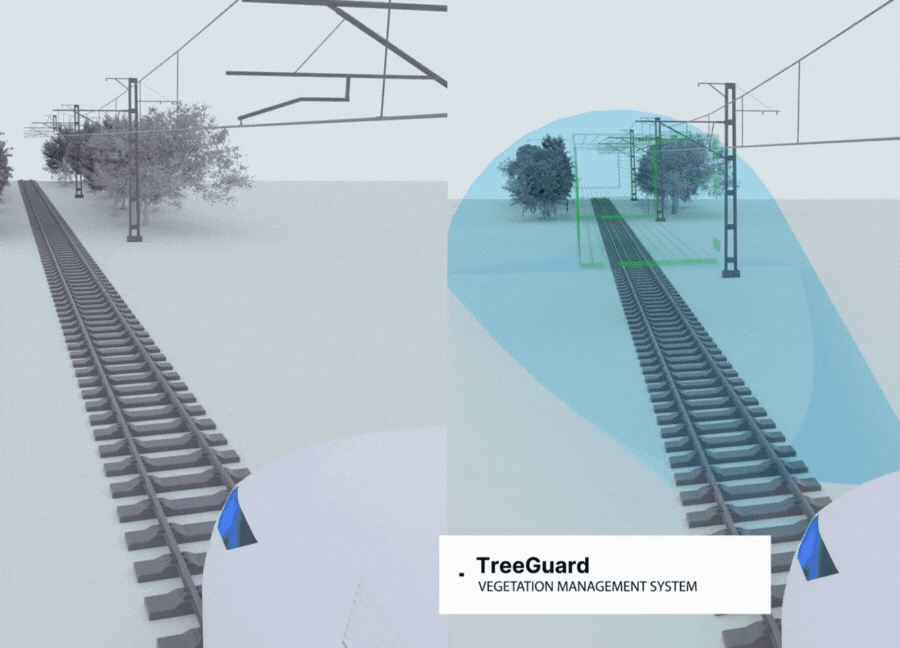
Recognized for its innovation, the Railway Vegetation Management System was awarded in both the Product Launches and Safety categories at the 2024 Railway Technology Excellence Awards, cementing its status as a game-changing solution for modern railway networks.
By integrating this system, railway operators can effectively manage vegetation, enhance infrastructure longevity, and maintain seamless operations.
Driving the future of Infrastructure Management
Kodifly’s digital twin technology redefines how infrastructure management is carried out. By automating data collection, enhancing monitoring capabilities, and offering predictive insights, we empower transport infrastructure operators to make informed decisions ensuring smarter and more sustainable infrastructure operations. Whether it's detecting intrusions, managing vegetation risks, or ensuring track stability, our solutions are a driving force for intelligent urban development.
Kodifly's Vision in Action
At Kodifly, digital twin technology is more than just a tool—it’s a key driver of our mission to revolutionize infrastructure management with safety, efficiency, and innovation at the forefront. We leverage digital twins to empower the world with unparalleled insights, transforming complex data into actionable solutions that drive results.
Success has never been more vividly realized than through the actionable insights unlocked by a dynamic, high-resolution point cloud.
With Kodifly, the future of smart infrastructure is already here.
Want to leverage the power of digital twins for your infrastructure management?
How many times have you wished you could find the optimum solution to a problem without having to try and err? Enter Digital Twin Technology - a revolutionary tool that creates real -time, dynamic replicas of physical systems allowing you to explore choices and predict outcomes with unparalleled accuracy.
The concept traces its roots back to NASA in the 1960s when they pioneered “mirroring technology” to create physical replicas of their space systems. In a landmark moment, the “Apollo 13” space mission in 1970 used fifteen simulators to virtually create and assess a moon-landing. As a result, the mission was aborted and the crew guided back to the safety of Earth. This was the first time in history that digital twin technology saved the day. Today, digital twins have evolved far beyond those early applications, transforming industries with real-time data integration and advanced analytics.
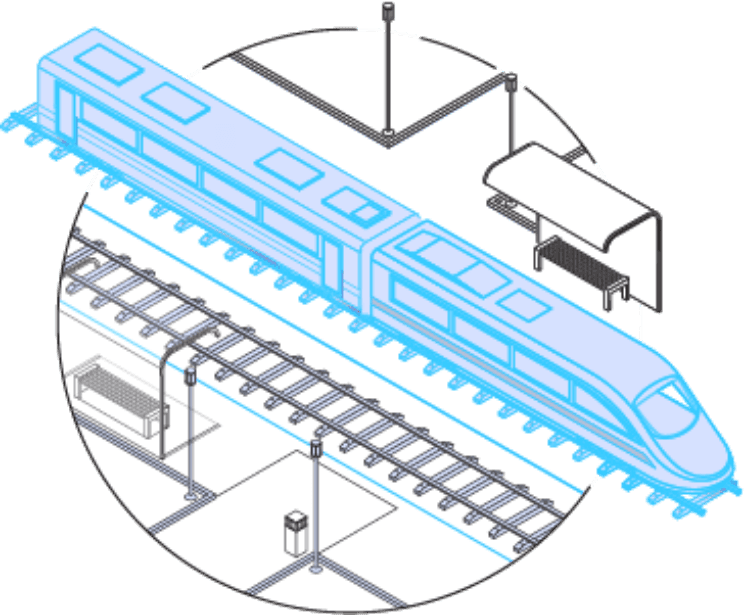
What is a Digital Twin?
A Digital Twin is more than just a virtual replica of real-world objects, systems, environments or even people. It’s a constantly evolving, real-time model powered by data from sensors, IoT devices, and advanced analytics. By mirroring its physical counterpart in a digitally curated environment, a digital twin enables organizations to simulate dynamic real-world scenarios, predict outcomes, and optimize performance.
What is a Spatial Digital Twin?
A Spatial Digital Twin takes this a step further by integrating spatial data into the digital model. Unlike a standard digital twin, it creates a location-based, highly detailed 3D representation of environments. Using tools like GNSS, LiDAR and camera technologies, spatial twins allow the capturing of the geometry, positioning and context of physical assets. This makes them invaluable for industries such as infrastructure, where precise spatial details are critical for decision making.
For instance, Kodifly uses spatial twins to model railway systems including tracks, tunnels, and surrounding vegetation. The technology not only mirrors physical structures but also provides actionable insights by analyzing real-time data.
How does Digital Twin Technology work?
The lifecycle of a digital twin starts with data collection. Sensors and IoT devices like LiDAR, cameras, and temperature gauges capture detailed real-world data about an asset’s structural performance, system operations, or environmental conditions.
This data is then transmitted via cloud platforms, edge computing, or wireless networks to centralized advanced software systems. The software processes and integrates the data to create an accurate digital replica (twin).
The twin is continuously updated with live data, ensuring it mirrors any changes in its physical counterpart. AI models analyze the data for patterns, inefficiencies, or potential anomalies. Insights from the analysis are then fed back into the system, allowing for constant refinement and optimization by creating a feedback loop.
This closed-loop system makes digital twins dynamic, allowing businesses to make proactive, data-driven decisions.
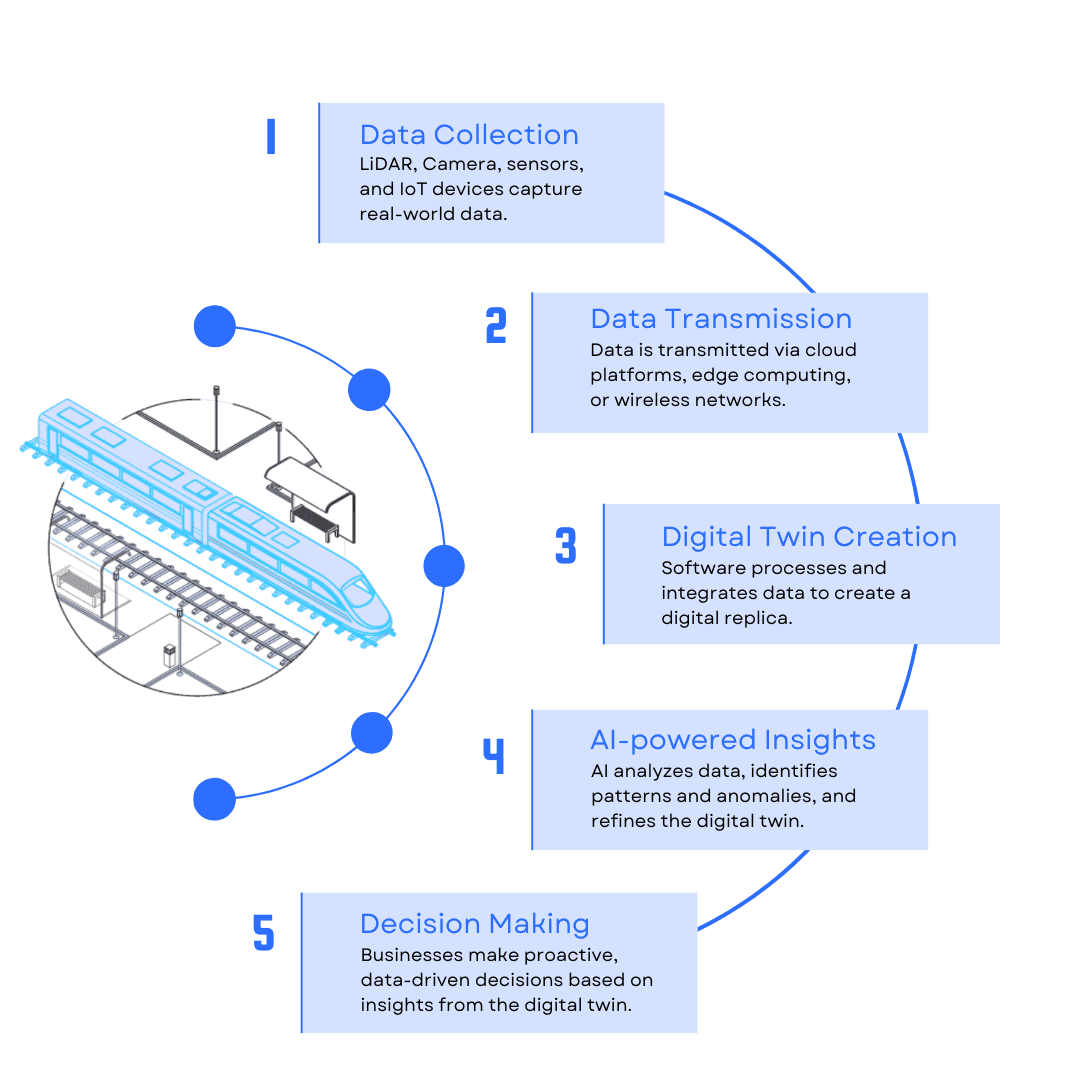
How is Digital Twin different from simulations?
While digital twins may sound similar to simulations, the two are fundamentally different. A simulation is a standalone model that tests specific scenarios and does not update in real time. A digital twin on the other hand, is a dynamic, real-time virtual replica that keeps getting updated, allowing for highly accurate predictions, identification of inefficiencies, and anticipation of failure (or success!)
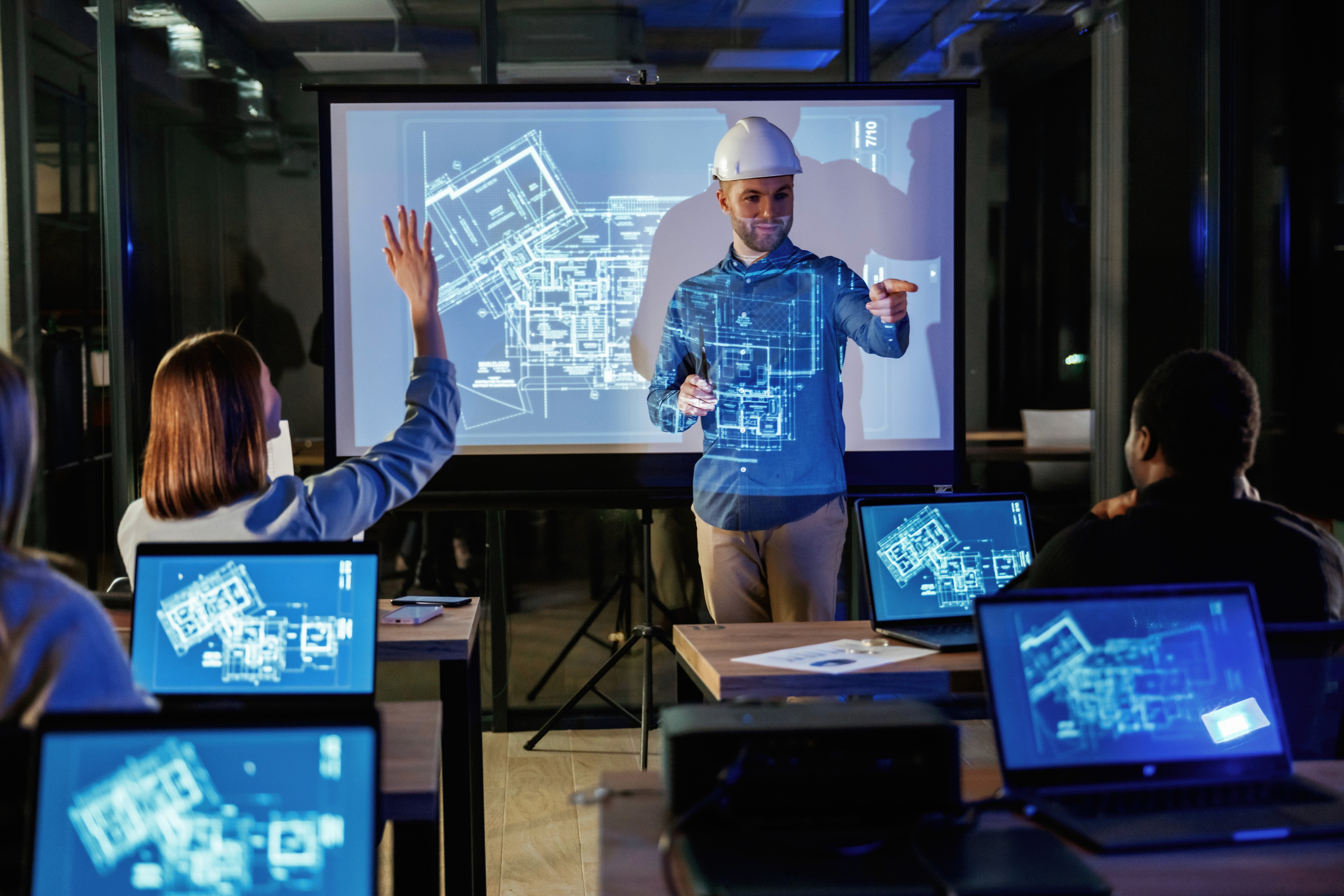
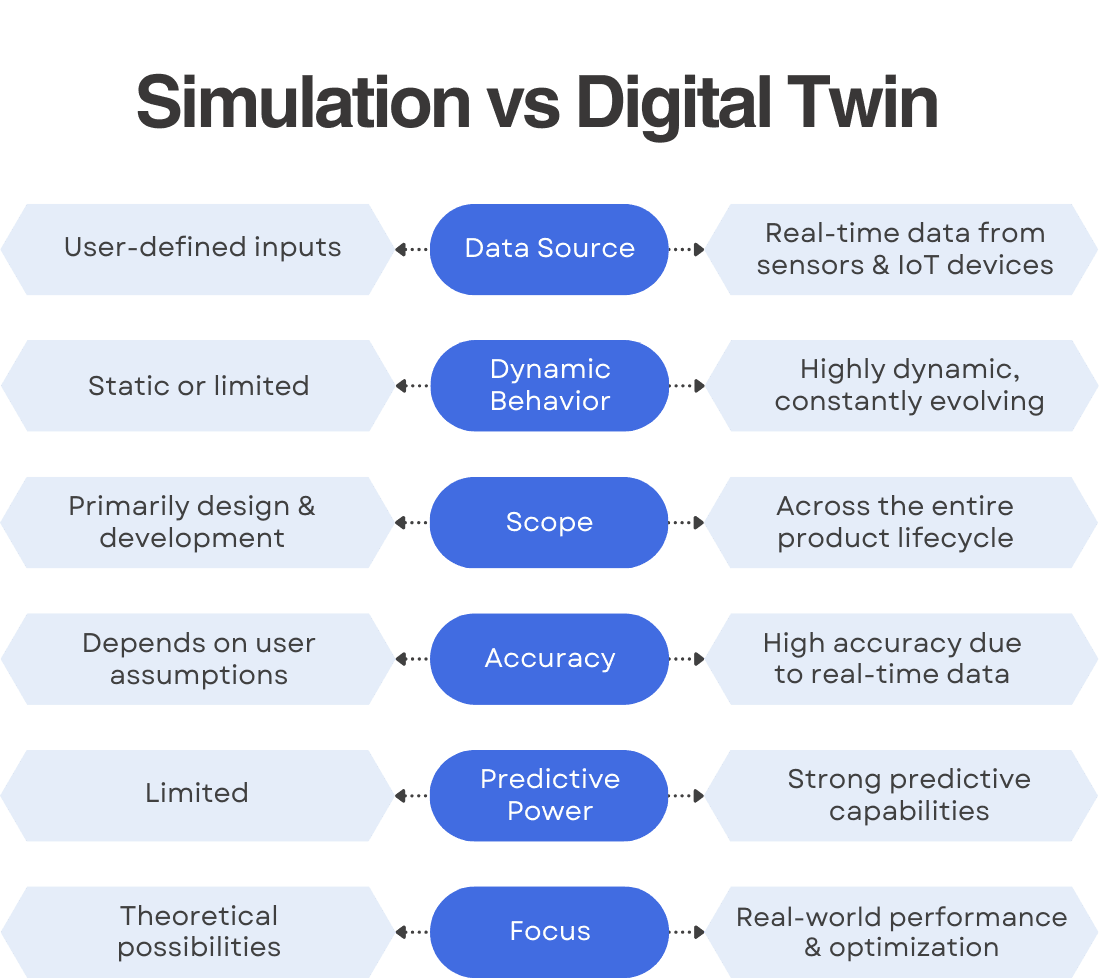
Where is Digital Twin technology used?
Digital twin technology spans a wide range of applications, proving its versatility and transformative potential. It encompasses various types, including Product Twins, System Twins, Data Twins, and Process Twins, each tailored to specific needs. From the initial ideation phase through engineering, production, control and monitoring the digital twin helps build and improve products and systems each step of the way.
In the manufacturing industry, digital twins test and validate new designs before they are sent to production, ensuring efficiency and reducing errors. The automotive, aerospace and defense industries are pioneers in making use of the digital twin for the ideation and development of successful new products. As industries evolve, the infrastructure and energy sectors are also poised to derive significant benefits from the technology. For instance, infrastructure projects can use digital twins to predict risks, enhance performance, and streamline operations, while energy systems may leverage them to optimize production and improve grid management.
By enabling improved performance, preemptive risk management and production optimization, digital twin technology is shaping the future of industries, offering tools to not only react to challenges but anticipate and address them proactively.
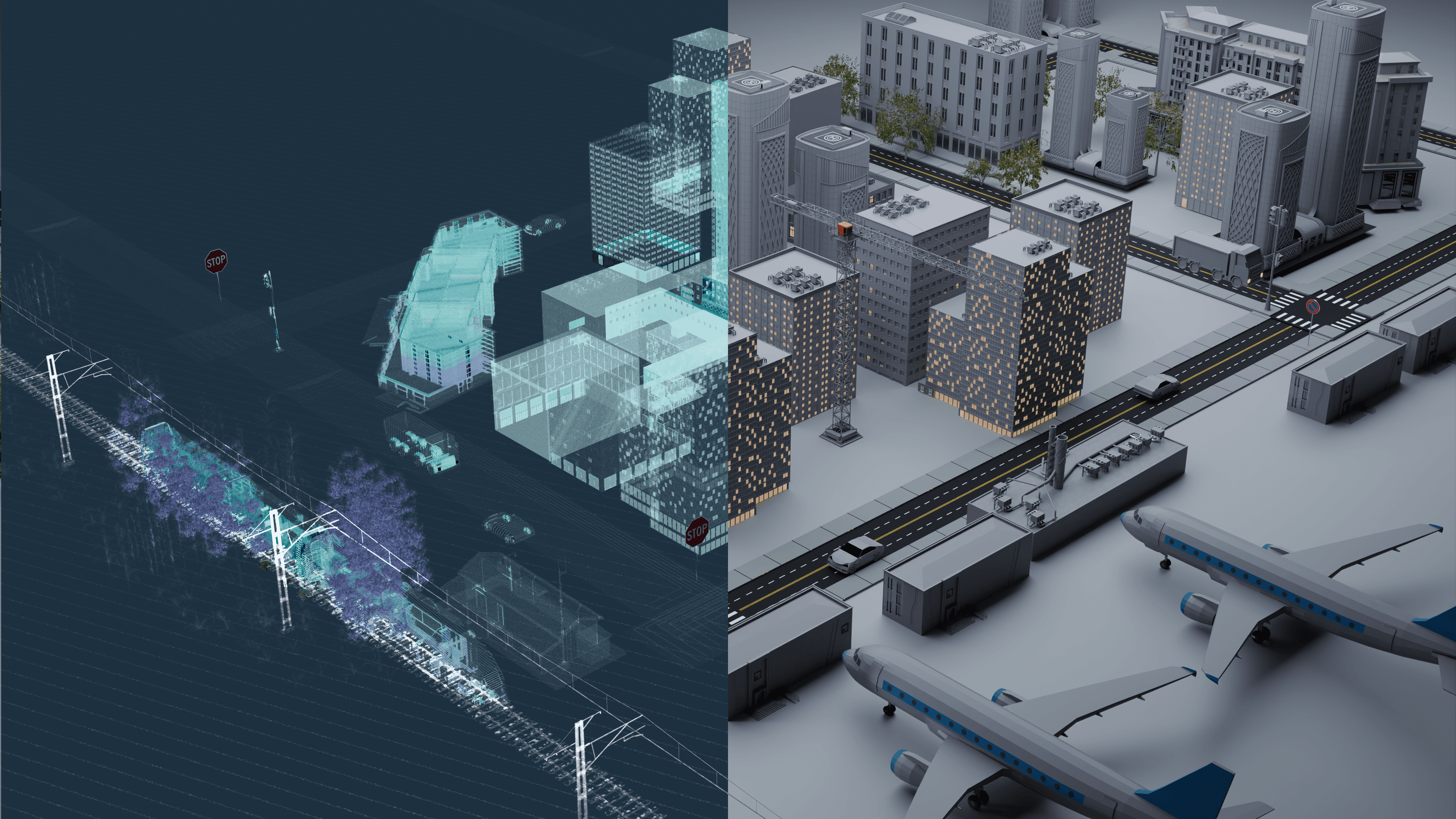
Kodifly leverages Digital Twin technology
Kodifly specializes in harnessing spatial digital twin technology to revolutionize infrastructure management in railways, highways, and airports. By integrating cutting-edge tools like LiDAR, GNSS positioning, and camera fusion technology, we provide transformative solutions for managing complex environments with precision and efficiency.
Kodifly’s SpatialSense Suite offers comprehensive solutions for capturing, processing, and analyzing spatial data. This platform combines inputs from LiDAR sensors, high-definition cameras, GPS, and IMUs to create highly accurate, real-time digital replicas of physical environments. These digital twins generate AI-powered actionable insights that empower infrastructure operators to make data-driven decisions, improve asset performance, and reduce maintenance costs.
For instance, Kodifly’s Railway Vegetation Management System is an advanced solution designed to ensure the safety and efficiency of railway operations by addressing vegetation-related challenges. Utilizing cutting-edge technologies such as LiDAR, AI-powered analytics, and GNSS positioning, the system provides railway operators with a comprehensive, automated approach to managing vegetation encroachment.
This system works by scanning and mapping the railway corridor in high detail, using LiDAR sensors to create precise 3D models of the surrounding environment. These models, combined with camera fusion technology, enable the system to identify vegetation intrusions that could interfere with the railway’s Kinetic Envelope (KE), signaling equipment, or power lines.
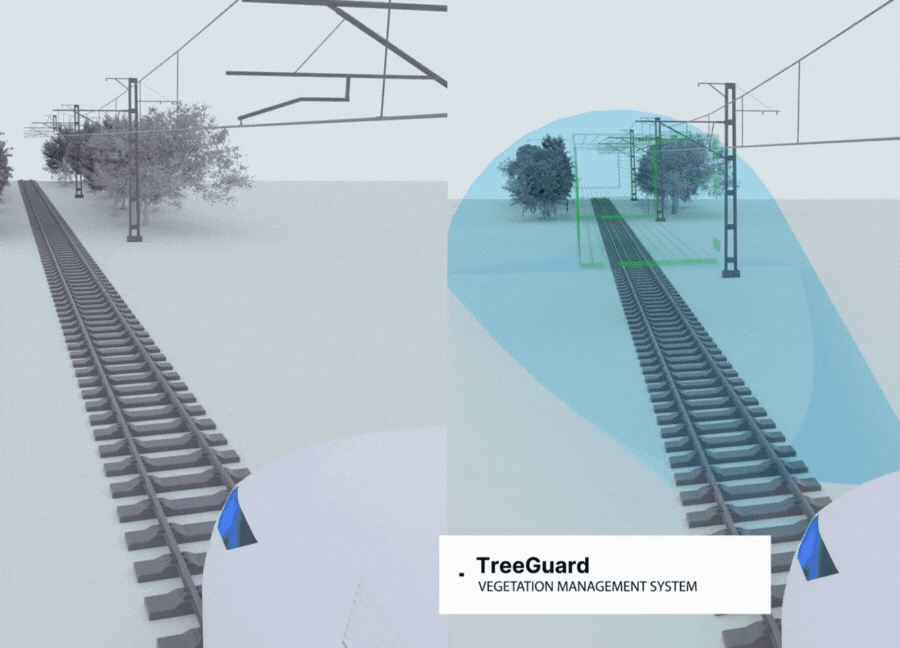
Recognized for its innovation, the Railway Vegetation Management System was awarded in both the Product Launches and Safety categories at the 2024 Railway Technology Excellence Awards, cementing its status as a game-changing solution for modern railway networks.
By integrating this system, railway operators can effectively manage vegetation, enhance infrastructure longevity, and maintain seamless operations.
Driving the future of Infrastructure Management
Kodifly’s digital twin technology redefines how infrastructure management is carried out. By automating data collection, enhancing monitoring capabilities, and offering predictive insights, we empower transport infrastructure operators to make informed decisions ensuring smarter and more sustainable infrastructure operations. Whether it's detecting intrusions, managing vegetation risks, or ensuring track stability, our solutions are a driving force for intelligent urban development.
Kodifly's Vision in Action
At Kodifly, digital twin technology is more than just a tool—it’s a key driver of our mission to revolutionize infrastructure management with safety, efficiency, and innovation at the forefront. We leverage digital twins to empower the world with unparalleled insights, transforming complex data into actionable solutions that drive results.
Success has never been more vividly realized than through the actionable insights unlocked by a dynamic, high-resolution point cloud.
With Kodifly, the future of smart infrastructure is already here.
Want to leverage the power of digital twins for your infrastructure management?
How many times have you wished you could find the optimum solution to a problem without having to try and err? Enter Digital Twin Technology - a revolutionary tool that creates real -time, dynamic replicas of physical systems allowing you to explore choices and predict outcomes with unparalleled accuracy.
The concept traces its roots back to NASA in the 1960s when they pioneered “mirroring technology” to create physical replicas of their space systems. In a landmark moment, the “Apollo 13” space mission in 1970 used fifteen simulators to virtually create and assess a moon-landing. As a result, the mission was aborted and the crew guided back to the safety of Earth. This was the first time in history that digital twin technology saved the day. Today, digital twins have evolved far beyond those early applications, transforming industries with real-time data integration and advanced analytics.
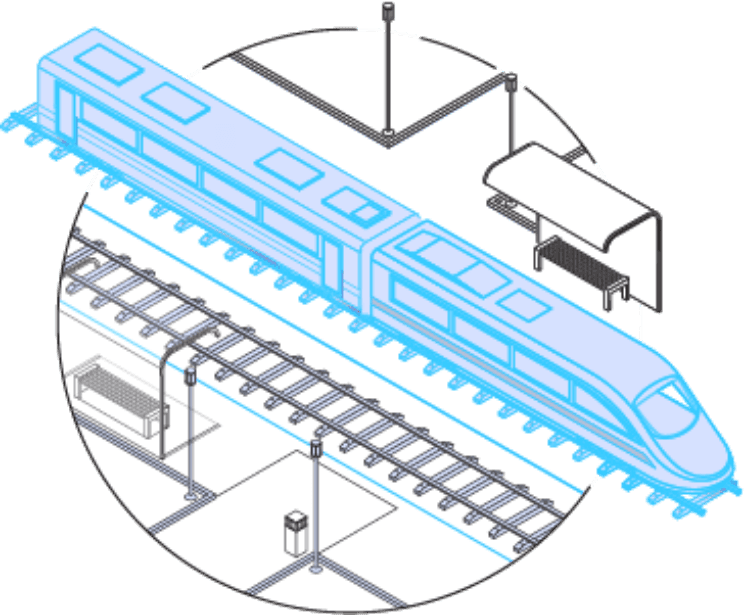
What is a Digital Twin?
A Digital Twin is more than just a virtual replica of real-world objects, systems, environments or even people. It’s a constantly evolving, real-time model powered by data from sensors, IoT devices, and advanced analytics. By mirroring its physical counterpart in a digitally curated environment, a digital twin enables organizations to simulate dynamic real-world scenarios, predict outcomes, and optimize performance.
What is a Spatial Digital Twin?
A Spatial Digital Twin takes this a step further by integrating spatial data into the digital model. Unlike a standard digital twin, it creates a location-based, highly detailed 3D representation of environments. Using tools like GNSS, LiDAR and camera technologies, spatial twins allow the capturing of the geometry, positioning and context of physical assets. This makes them invaluable for industries such as infrastructure, where precise spatial details are critical for decision making.
For instance, Kodifly uses spatial twins to model railway systems including tracks, tunnels, and surrounding vegetation. The technology not only mirrors physical structures but also provides actionable insights by analyzing real-time data.
How does Digital Twin Technology work?
The lifecycle of a digital twin starts with data collection. Sensors and IoT devices like LiDAR, cameras, and temperature gauges capture detailed real-world data about an asset’s structural performance, system operations, or environmental conditions.
This data is then transmitted via cloud platforms, edge computing, or wireless networks to centralized advanced software systems. The software processes and integrates the data to create an accurate digital replica (twin).
The twin is continuously updated with live data, ensuring it mirrors any changes in its physical counterpart. AI models analyze the data for patterns, inefficiencies, or potential anomalies. Insights from the analysis are then fed back into the system, allowing for constant refinement and optimization by creating a feedback loop.
This closed-loop system makes digital twins dynamic, allowing businesses to make proactive, data-driven decisions.
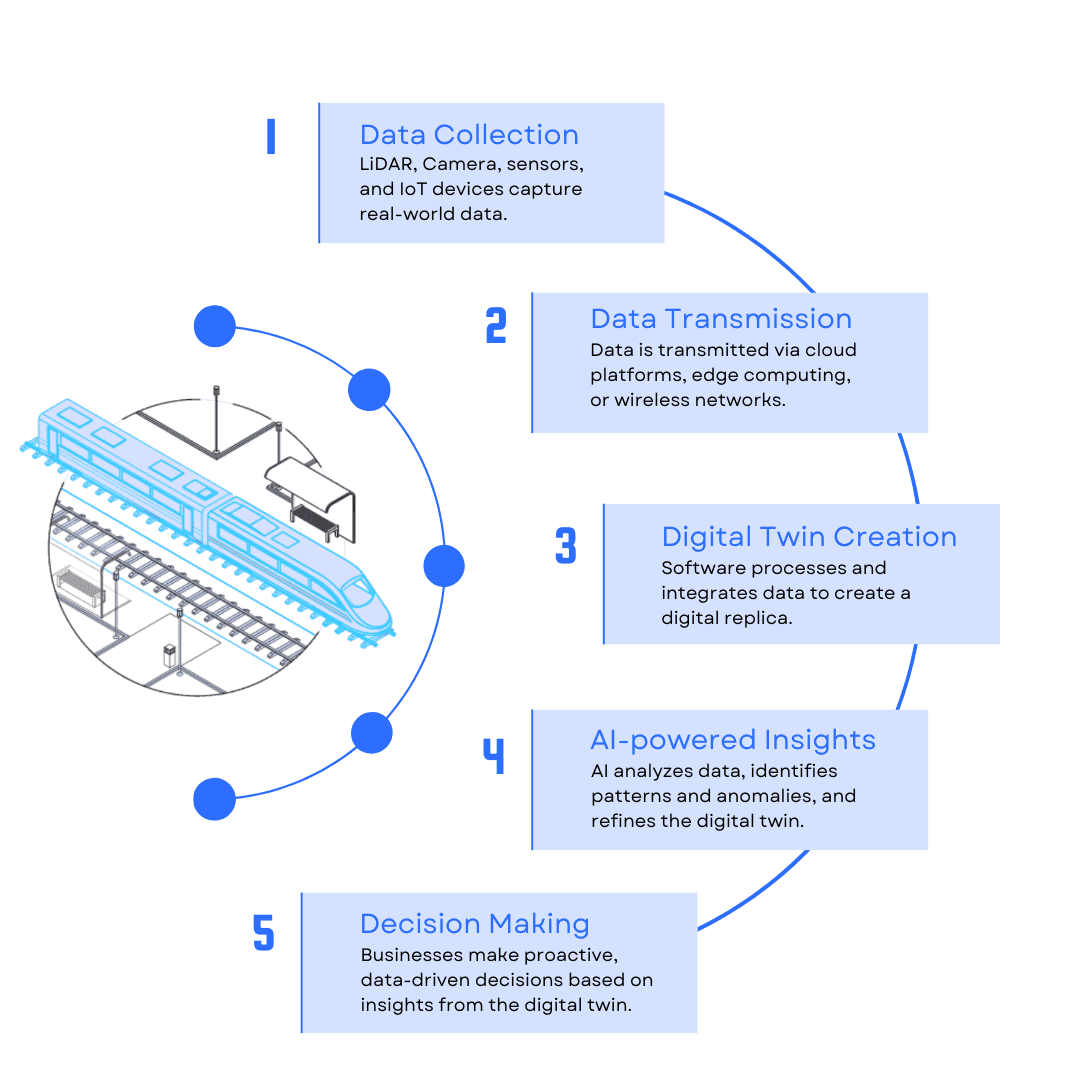
How is Digital Twin different from simulations?
While digital twins may sound similar to simulations, the two are fundamentally different. A simulation is a standalone model that tests specific scenarios and does not update in real time. A digital twin on the other hand, is a dynamic, real-time virtual replica that keeps getting updated, allowing for highly accurate predictions, identification of inefficiencies, and anticipation of failure (or success!)
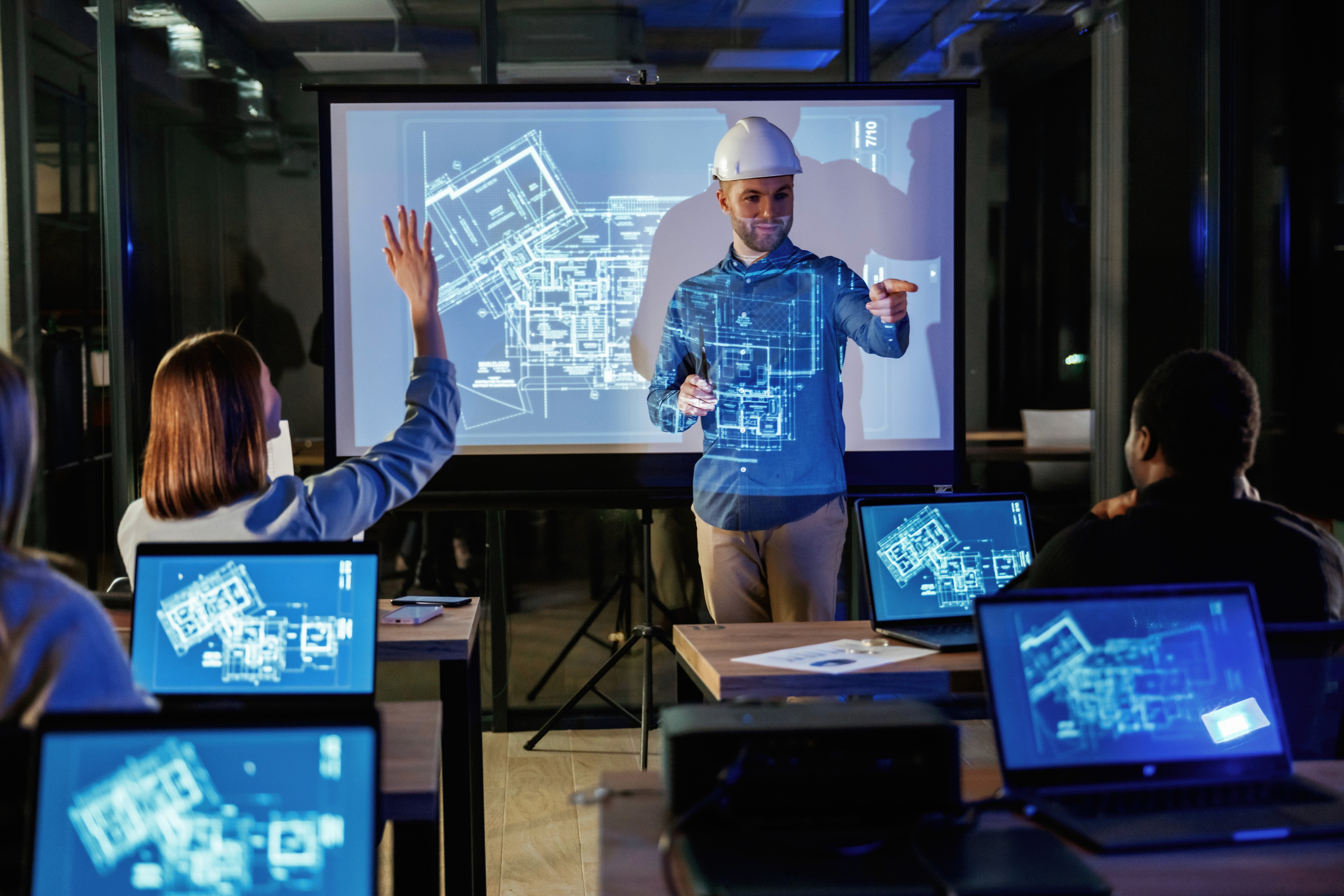
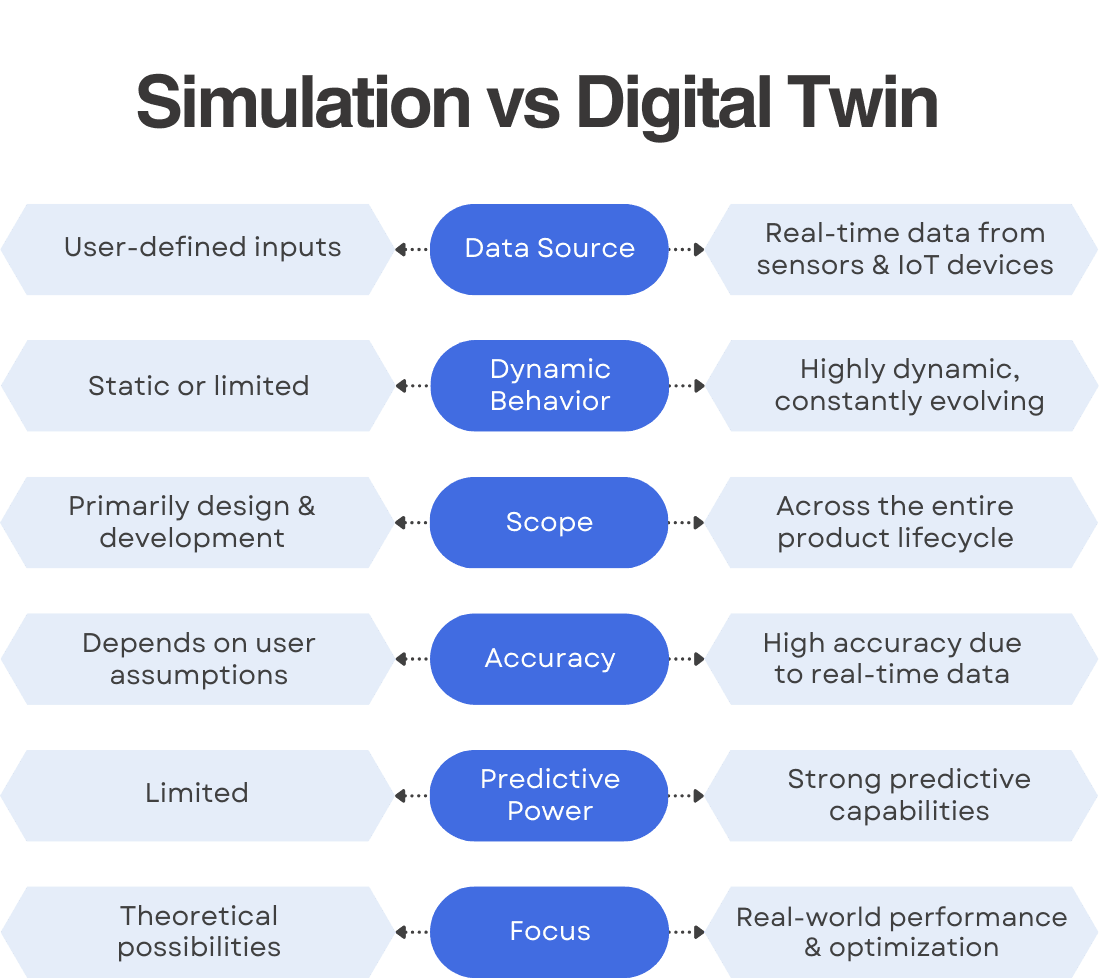
Where is Digital Twin technology used?
Digital twin technology spans a wide range of applications, proving its versatility and transformative potential. It encompasses various types, including Product Twins, System Twins, Data Twins, and Process Twins, each tailored to specific needs. From the initial ideation phase through engineering, production, control and monitoring the digital twin helps build and improve products and systems each step of the way.
In the manufacturing industry, digital twins test and validate new designs before they are sent to production, ensuring efficiency and reducing errors. The automotive, aerospace and defense industries are pioneers in making use of the digital twin for the ideation and development of successful new products. As industries evolve, the infrastructure and energy sectors are also poised to derive significant benefits from the technology. For instance, infrastructure projects can use digital twins to predict risks, enhance performance, and streamline operations, while energy systems may leverage them to optimize production and improve grid management.
By enabling improved performance, preemptive risk management and production optimization, digital twin technology is shaping the future of industries, offering tools to not only react to challenges but anticipate and address them proactively.
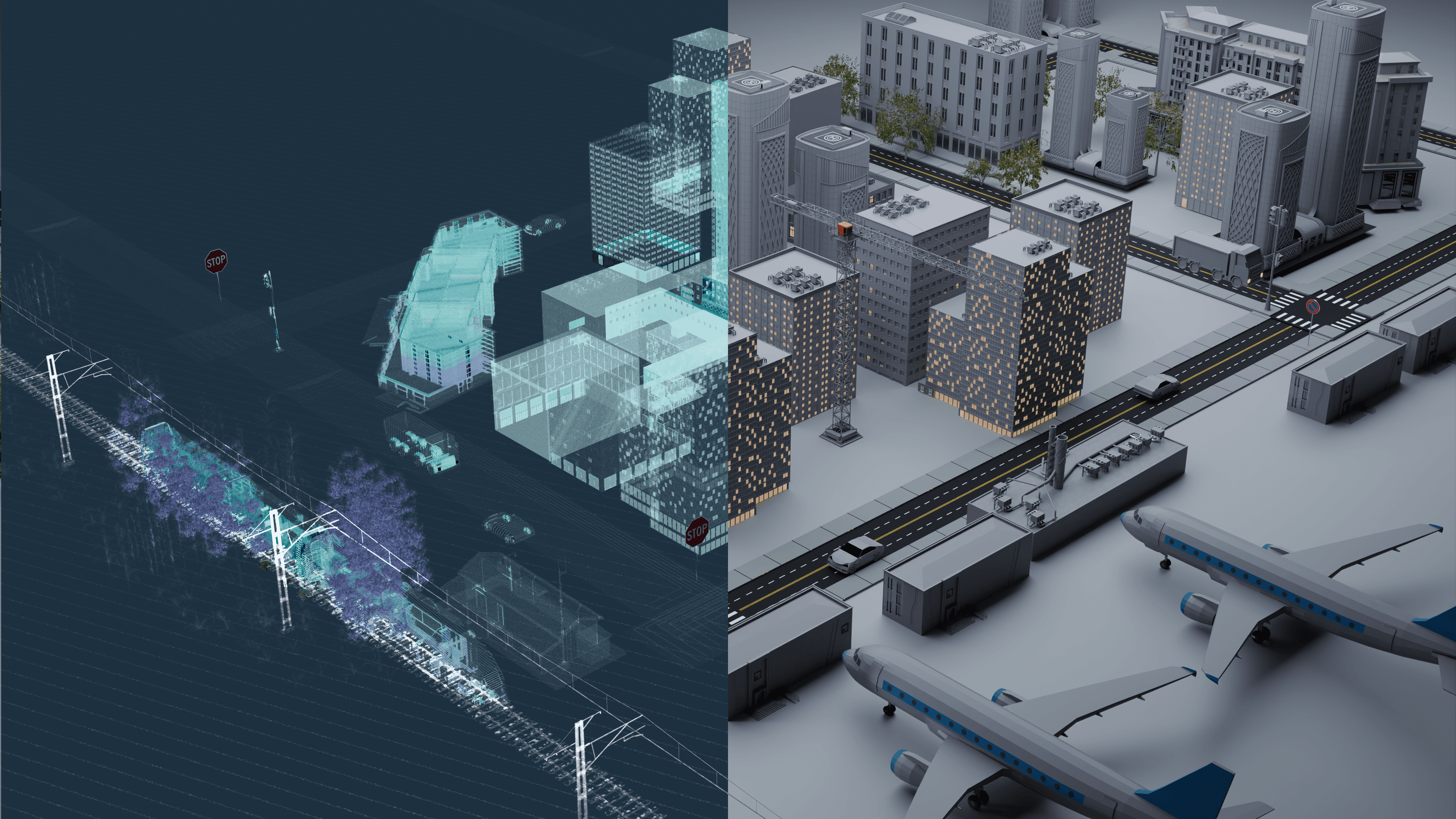
Kodifly leverages Digital Twin technology
Kodifly specializes in harnessing spatial digital twin technology to revolutionize infrastructure management in railways, highways, and airports. By integrating cutting-edge tools like LiDAR, GNSS positioning, and camera fusion technology, we provide transformative solutions for managing complex environments with precision and efficiency.
Kodifly’s SpatialSense Suite offers comprehensive solutions for capturing, processing, and analyzing spatial data. This platform combines inputs from LiDAR sensors, high-definition cameras, GPS, and IMUs to create highly accurate, real-time digital replicas of physical environments. These digital twins generate AI-powered actionable insights that empower infrastructure operators to make data-driven decisions, improve asset performance, and reduce maintenance costs.
For instance, Kodifly’s Railway Vegetation Management System is an advanced solution designed to ensure the safety and efficiency of railway operations by addressing vegetation-related challenges. Utilizing cutting-edge technologies such as LiDAR, AI-powered analytics, and GNSS positioning, the system provides railway operators with a comprehensive, automated approach to managing vegetation encroachment.
This system works by scanning and mapping the railway corridor in high detail, using LiDAR sensors to create precise 3D models of the surrounding environment. These models, combined with camera fusion technology, enable the system to identify vegetation intrusions that could interfere with the railway’s Kinetic Envelope (KE), signaling equipment, or power lines.
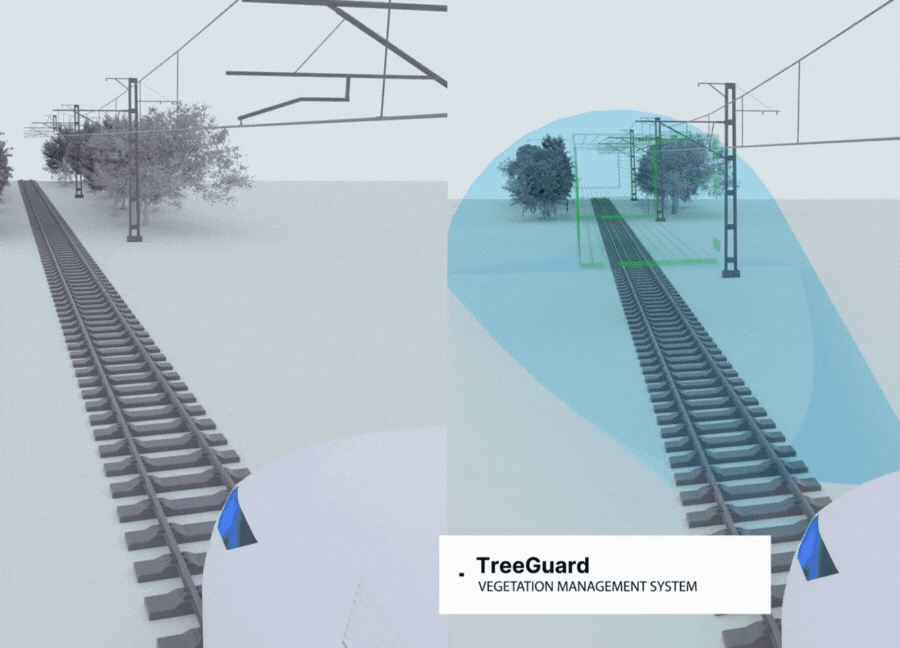
Recognized for its innovation, the Railway Vegetation Management System was awarded in both the Product Launches and Safety categories at the 2024 Railway Technology Excellence Awards, cementing its status as a game-changing solution for modern railway networks.
By integrating this system, railway operators can effectively manage vegetation, enhance infrastructure longevity, and maintain seamless operations.
Driving the future of Infrastructure Management
Kodifly’s digital twin technology redefines how infrastructure management is carried out. By automating data collection, enhancing monitoring capabilities, and offering predictive insights, we empower transport infrastructure operators to make informed decisions ensuring smarter and more sustainable infrastructure operations. Whether it's detecting intrusions, managing vegetation risks, or ensuring track stability, our solutions are a driving force for intelligent urban development.
Kodifly's Vision in Action
At Kodifly, digital twin technology is more than just a tool—it’s a key driver of our mission to revolutionize infrastructure management with safety, efficiency, and innovation at the forefront. We leverage digital twins to empower the world with unparalleled insights, transforming complex data into actionable solutions that drive results.
Success has never been more vividly realized than through the actionable insights unlocked by a dynamic, high-resolution point cloud.
With Kodifly, the future of smart infrastructure is already here.
Want to leverage the power of digital twins for your infrastructure management?
Table of Content
Dec 26, 2024
Interested to find out how Kodifly transforms the infrastructure space?

Why Waiting to Adopt Technology is No Longer an option, It's a Risk
Aug 19, 2025

Smarter Cities Start Here! The Role of AI in Infrastructure Management
Aug 11, 2025

Rework is Killing Your Margins : How Real-Time Monitoring Can Save You Millions
Aug 5, 2025

Inside New Murabba: Constructing Riyadh’s Futuristic Downtown
Jul 22, 2025